Self-tapping screws are specialized fasteners widely used in various industries and applications, ranging from construction and automotive to electronics and furniture assembly. These screws are designed with unique features that enable them to create their own threads as they are driven into a material, eliminating the need for pre-drilling or tapping holes.
At first glance, self-tapping screws may appear similar to regular screws, but upon closer examination, one can identify their distinct characteristics. The most notable difference lies in the design of the screw's tip. Self-tapping screws have a sharp, pointed end, often with a flute-like structure or a set of specially shaped threads called "cutting threads."
The process of how self-tapping screws work can be summarized in a few simple steps. Firstly, the screw's sharp point allows it to pierce through the material's surface easily. As the screw is rotated, the cutting threads or flute-like structure help to carve a path by removing the material, creating a helical thread. This continuous rotation and axial force facilitate the screw's penetration into the material.
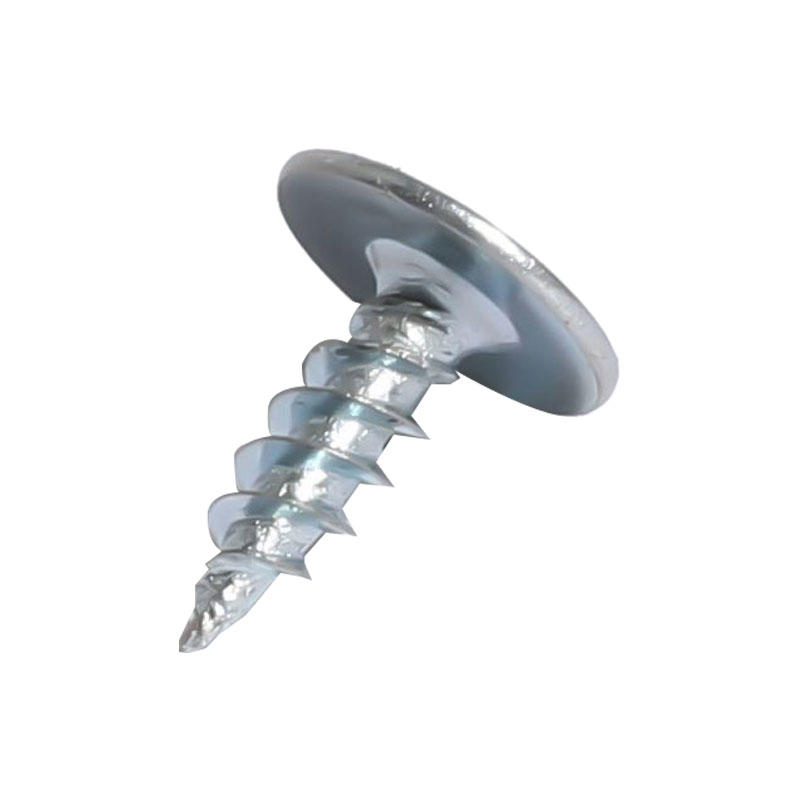
The success of
self-tapping screws is attributed to their ability to form threads within the material. The cutting threads on the screw act as small blades, cutting through the material's fibers or particles as they rotate. These threads also help to carry the debris out of the hole, preventing clogging and allowing the screw to advance smoothly.
The creation of threads by self-tapping screws depends on the properties of the material being fastened. For softer materials like wood or certain plastics, the cutting threads can easily carve out a thread path, resulting in a secure and tight connection. In harder materials like metal, the cutting threads may struggle to create threads, requiring a higher rotational force and careful handling to avoid damaging the screw or the material.
To maximize the effectiveness of self-tapping screws, it is crucial to choose the appropriate screw size and thread design for the specific application. Screw size refers to the length and diameter of the screw, which should be matched to the material's thickness and the desired depth of penetration. The thread design, such as pitch and depth, should be selected based on the material's properties and the desired level of thread engagement.
Self-tapping screws come in a variety of head types, including flat, pan, oval, and hex, allowing for different applications and aesthetics. Additionally, they can be manufactured from various materials, such as steel, stainless steel, or non-ferrous metals, to provide corrosion resistance and strength suitable for the intended use.
In summary, self-tapping screws are versatile fasteners designed to create their own threads as they are driven into a material. Through the use of cutting threads or a flute-like structure, these screws are able to remove material and form threads, providing a secure and reliable connection. Their ability to eliminate the need for pre-drilling or tapping holes makes them a popular choice in many industries, streamlining the assembly process and improving efficiency.