The quality of electroplated products should be controlled from the appearance and other aspects. The surface of the product is not allowed to have no local plating, scorching, roughness, gray, peeling, crust condition and streaking, not allowed to have pockmark, black plating slag, passivation film loose, off and serious passivation traces.
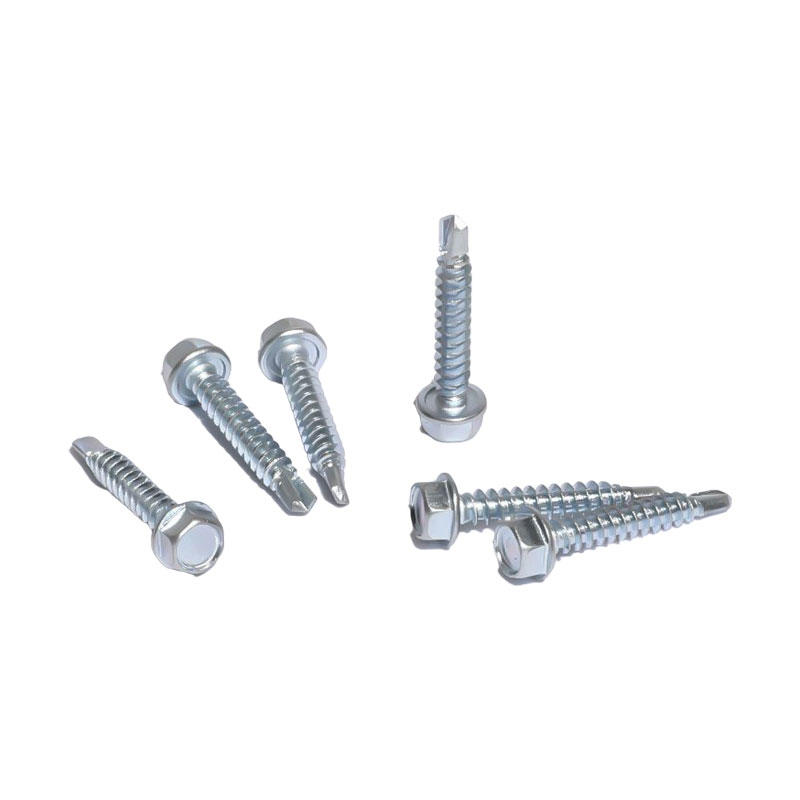
When the fastener is tightened, the hydrogen turns enough toward the part where the stress is concentrated, causing the pressure to increase beyond the strength of the base metal and producing a small surface rupture. Hydrogen is active and quickly penetrates into the newly formed fracture. This pressure-rupture-infiltration cycle continues until the fastener fractures.
It usually occurs within a few hours of the initial stress application, and the way the coating collects on the fastener surface varies with different deposition methods. To eliminate the threat of hydrogen embrittlement, fasteners are heated and baked as quickly as possible after plating to allow hydrogen to leach out of the coating, with baking typically occurring at 375-4000F (176-190°C) for 3-24 hours.